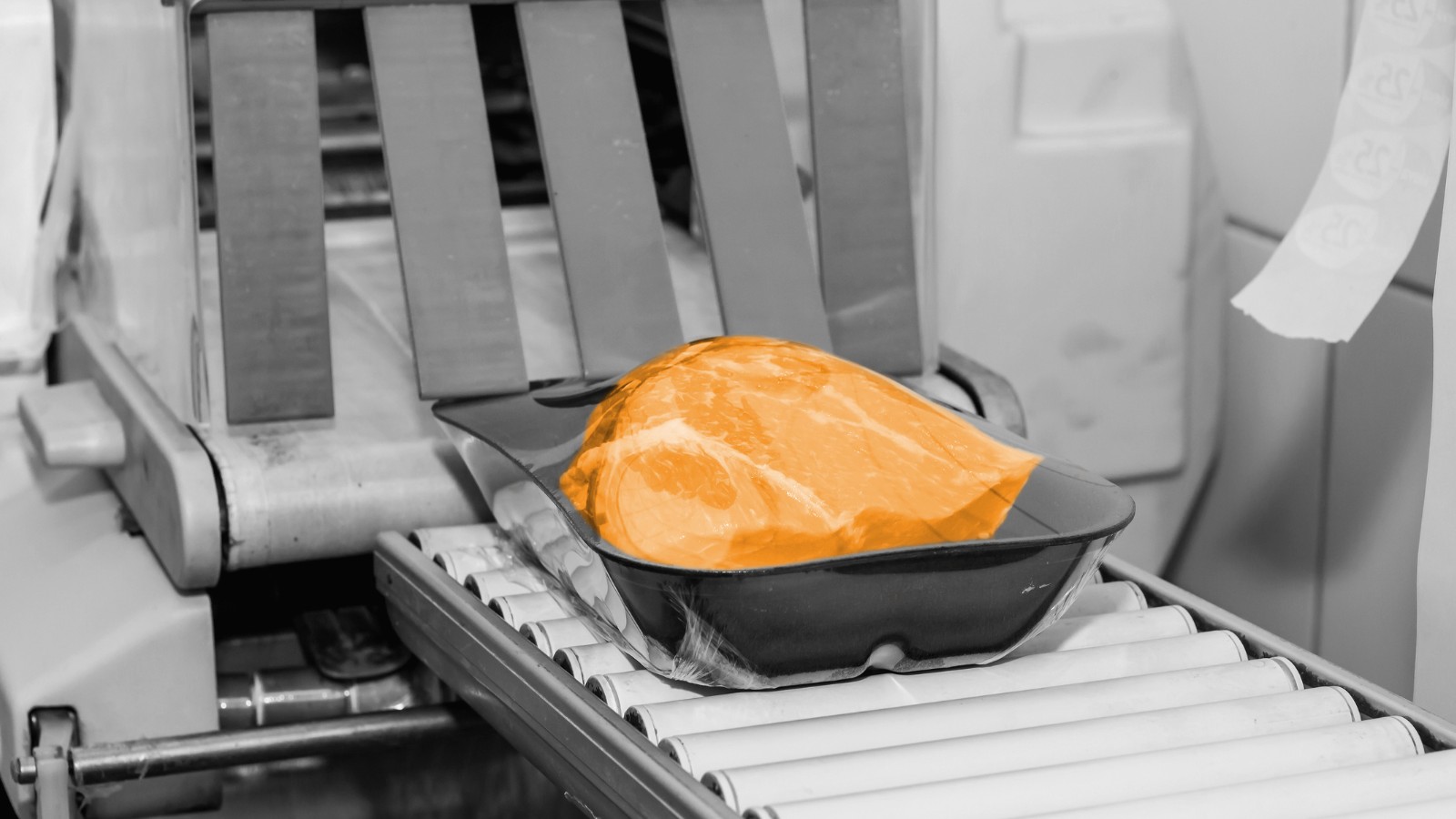
Delivering targeted interventions that result in measurable improvements is essential for any organisation looking to enhance operational performance. One of our previous projects involved working with a leading food producer in Europe to transform leadership capabilities and improve line performance across multiple sites. This post explores the challenges, solutions implemented, and the significant outcomes we achieved.
Our client, a leading producer of beef, pork, chicken, and convenience products, was facing significant operational issues across its UK facilities. One site, in particular, a sliced cooked meats plant, was experiencing a weekly financial loss of approximately £195,000. The company was also dealing with inefficient factory layouts, excessive raw material waste, and low engagement between cross-functional teams. These issues were compounded by poor customer satisfaction due to a high number of complaints, making it clear that sustainable improvements were urgently needed.
Challenges
Several critical issues were identified during the initial analysis:
- Operational Inefficiencies: Factory layouts were inefficient, resulting in high levels of waste and poor visual controls for tracking material movement and setting priorities.
- Low Engagement: Engagement between operations and cross-functional teams was lacking, with little ownership of ideas at the shop-floor level.
- Directive Management Style: The existing management approach was more directive than collaborative, stifling innovation and failing to motivate employees to engage in continuous improvement.
- High Financial Losses: The sliced cooked meats plant, in particular, was losing approximately £195,000 per week, a situation made worse by poor-quality standards and repeat customer complaints.
Solutions
In response to these challenges, a comprehensive Lean Leadership Programme was designed and implemented. The programme focused on improving leadership skills and operational efficiency, with the initial deployment taking place at the sliced cooked meats plant and later expanding to seven other sites across the UK.
Key solutions included:
- Lean Leadership Academy (LLA): A training programme that engaged 52 operational leaders across various disciplines, including technical, engineering, logistics, and HR. This programme was instrumental in developing leadership skills and creating a culture of continuous improvement.
- Facility Layout Redesign: A detailed plan was developed to improve the layout and efficiency of the plant, reducing waste and improving material flow.
- Value Stream Mapping (VSM): This activity identified areas of waste within the processes and enabled the team to implement targeted improvements.
- Line Performance Improvements (LPI): Specific projects were undertaken to improve the performance of production lines across the UK sites.
- Continuous Improvement Team: A dedicated team was established by the client to sustain improvements and ensure ongoing collaboration across functions.
Impact on Performance
The outcomes of these interventions were substantial, leading to significant cost savings and operational improvements:
- £991,600 in Savings: Ideas generated through Value Stream Mapping activities were implemented, delivering nearly £1 million in savings.
- £2.4 Million in Cost Avoidance: The implementation of tactical initiatives across seven sites resulted in £2.4 million in cost avoidance.
- 66% Reduction in Weekly Losses: The financial losses at the sliced cooked meats plant were reduced by 66%, representing a major turnaround.
- Gold Standard Accreditation: The improved processes and leadership led to Gold Standard Accreditation for food production, allowing the client to engage with high-profile customers such as Marks & Spencer.
- 60% Reduction in Customer Complaints: By improving product quality and operational processes, customer complaints were reduced by 60%.
Final Thoughts
This project demonstrated the transformative power of strong leadership, efficient processes, and a collaborative culture. By investing in leadership development and continuous improvement, the client was able to not only reduce costs but also improve product quality and customer satisfaction. The success of this project highlights the importance of a holistic approach to operational excellence, where leadership and line performance go hand in hand to achieve sustainable results.
For more information on how similar interventions can help your organisation achieve operational excellence, feel free to contact us.