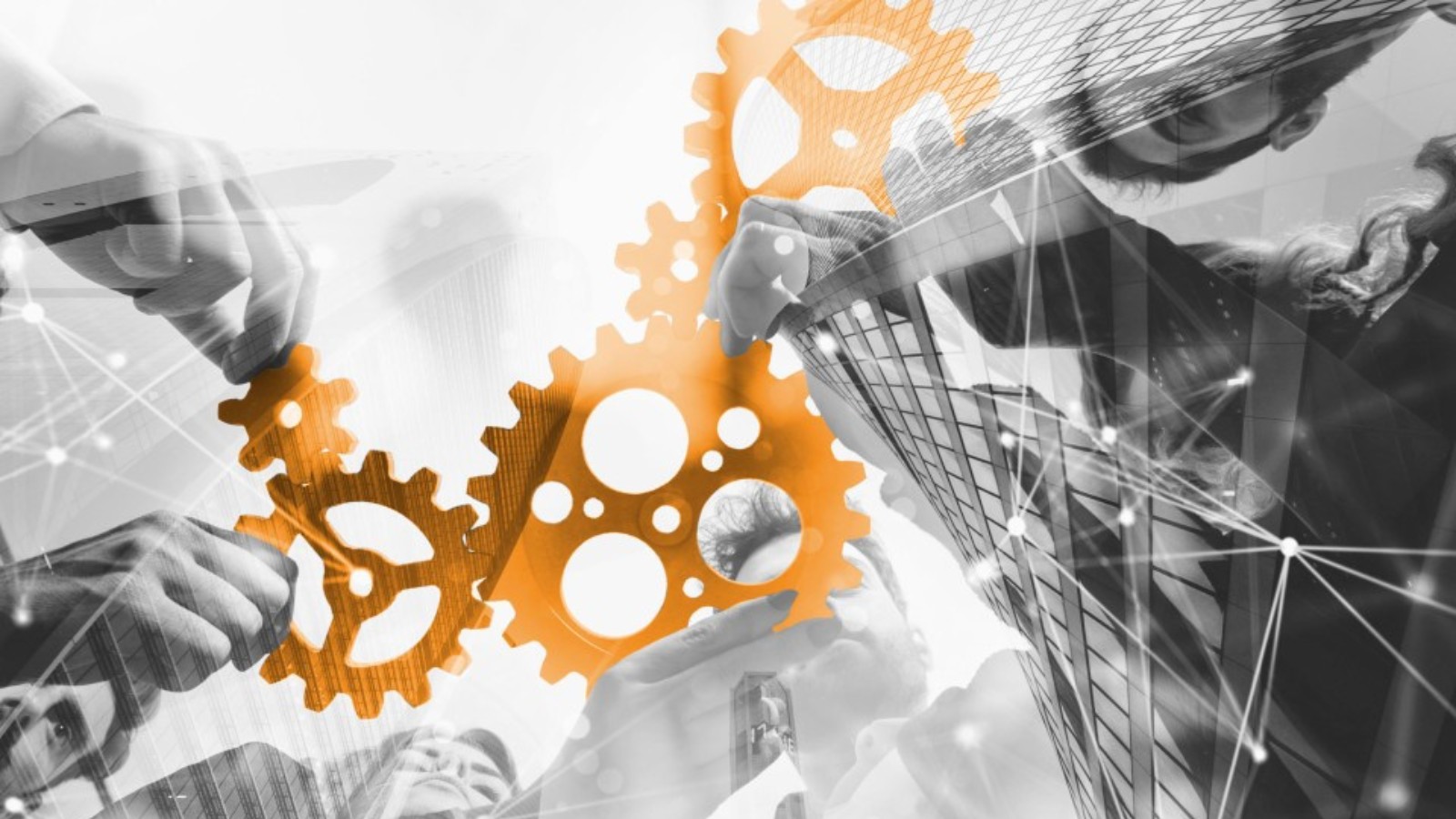
While lean methodologies emphasise process optimisation, the human element often proves to be the differentiating factor in achieving sustained quality improvements. This article suggests how effective utilisation of human capital will enhance overall quality outcomes and organisational performance. By highlighting the significance of empowering and engaging employees, this article contributes to a deeper understanding of the interplay between people and processes in lean manufacturing environments.
Amidst the emphasis on process optimisation, the role of people often tends to be overshadowed. The demands of employees for ethical and authentic leadership in a demonstrated culture of psychological safety and emotional intelligence in a developing world of Industry 5.0 is alien to many leaders, and confusing to others. This article aims to underscore the significance of people-centric approaches in driving right first-time quality outcomes within lean manufacturing frameworks.
Lean Manufacturing and Right First Time Quality
Lean manufacturing principles are centred on the relentless pursuit of perfection through waste reduction, continuous improvement, and the delivery of value to customers. While lean tools and techniques such as value stream mapping, 5S, and Kanban play a crucial role in streamlining processes and minimising defects, their effectiveness ultimately hinges on human involvement and decision-making to sustain the energy and intention of change. Employees are not merely cogs in the machine but rather active participants whose knowledge, skills, and commitment profoundly impact quality outcomes.
The Human Element in Lean Manufacturing
Firstly, let’s look at employee engagement. Engaged employees are more likely to take ownership of their work and strive for quality and operational excellence. For many years, the mantra has been “Treat people as you would expect to be treated,” this mantra has now changed to “Treat people as they expect to be treated.” This is not semantics but a very real need in 2024 and beyond to meet the expectations of Gen ‘Z’ and millennials in the workplace; I would argue that this should have always been so.
People expect to feel psychologically safe and heard in order to engage. They expect to contribute and have those contributions welcomed or at least be honestly and openly considered. Lean practitioners have always quoted one of the eight wastes in Lean as not using our people’s intellect, the difference now is that we must act on this awareness to retain our people; we have to put as much effort into our people as we do the established Lean tools. By fostering a culture of continuous improvement and providing avenues for employee involvement in problem-solving, organisations can harness the collective intelligence of their workforce to identify and address quality issues proactively.
Leadership and Communication
As a consultant I am asked to help businesses improve. Though this may be considered a bold statement, in probably 95% of the cases the issue that needs to improve always goes back to leadership. Effective leadership is instrumental in guiding teams towards quality objectives and fostering a shared sense of purpose. Clear communication channels facilitate the dissemination of quality-related information and enable employees to align their efforts with organisational goals, resulting in improved coordination and collaboration across departments; that is when the employees understand the goals, and the culture is such that the leadership removes the barriers in order that the employees can achieve the goals. But what I find so often is that middle level or even senior leadership have not been given the training, tools or skill sets by their leadership to be able to lead, to identify the goals, or how to remove the barriers by their leadership.
Leveraging Lean Tools with a People-Centric Approach
While lean tools and techniques provide valuable frameworks for process improvement, their successful implementation depends on the active involvement and commitment of employees at all levels of the organisation. For instance, implementing 5S principles requires not only rearranging workspaces but also instilling a culture of cleanliness and organisation through employee training and reinforcement, to sustain the change. Similarly, the success of a Kanban system relies on effective communication and collaboration among team members to ensure timely replenishment and movement of materials.
Dr W. E. Deming wrote about this in his 14 Principles of Continuous Improvement 70 years ago, which became the foundation of the famous Toyota Production System. Now even though the tools have been commonplace from his teachings for over half a century, how to get the best out of people is still not being held as having equal importance.
Conclusion
In conclusion, while lean manufacturing provides a structured approach to both quality and process optimisation, its effectiveness in delivering right first-time quality ultimately hinges on the active involvement, true engagement, and empowerment of people. By recognising employees as more than just ‘assets,’ but as enablers, and investing in their development, organisations can create a culture of quality excellence that permeates every aspect of their operations. It is imperative for organisations to strike a balance between process optimisation and people-centric approaches to maximise the benefits of lean manufacturing and drive sustainable quality improvements.