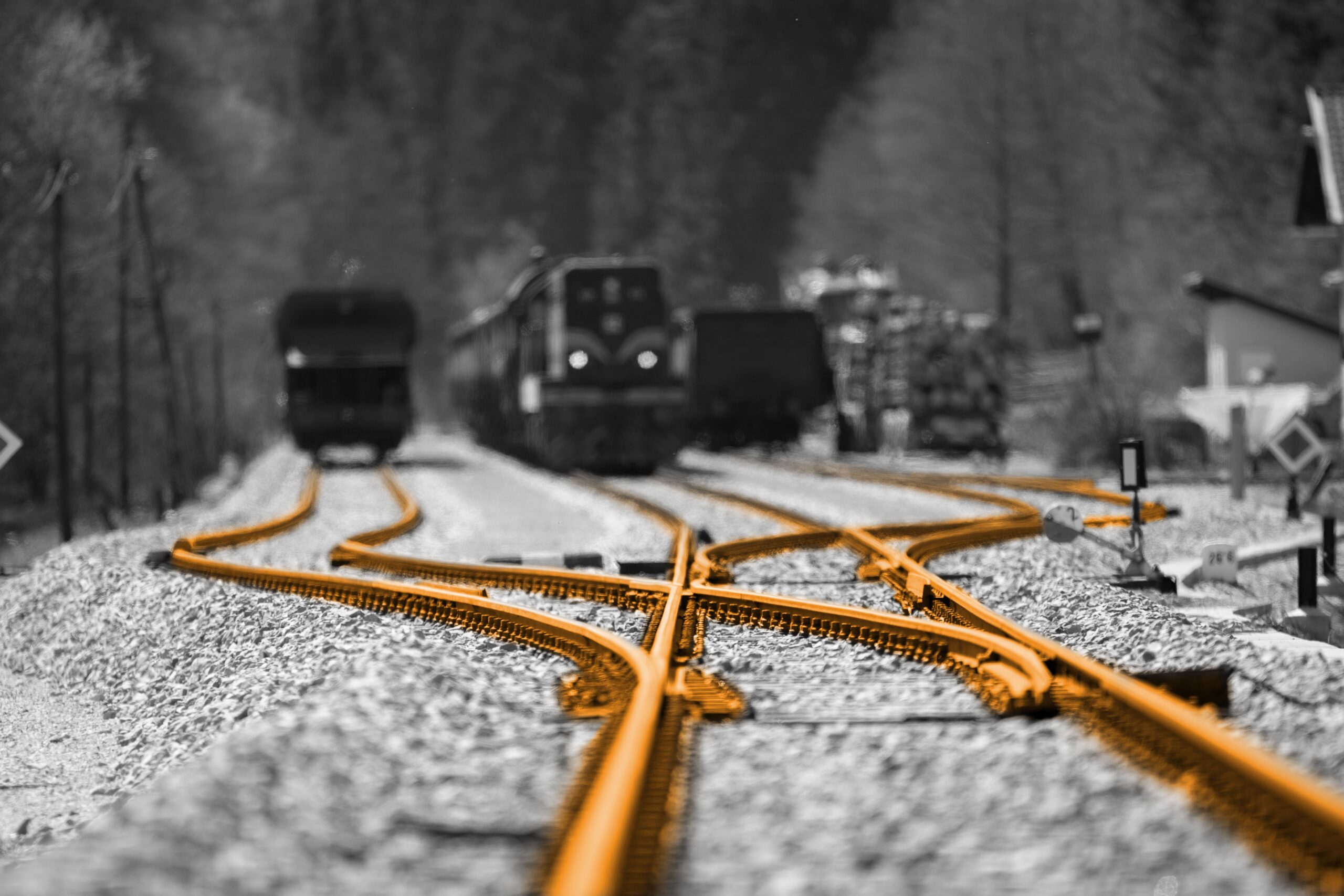
Outstations Performance Improvement
As part of DB Schenker’s Service Design Phase 2 Programme, out client identified that a significant shift in performance across its Maintenance Network was required. One element of this programme focused on the outstations who had been working in an isolated non structured manor with very little focus on structured improvement.
Outstations and their linked Maintenance Depots were selected due to their ability to effect train reliability and on time passage through the network.
Margam Knuckle Yard was one identified to lead in the implementation of a Continuous Improvement principles, systems and tool. Margam was selected due to its pivotal role in supporting Trains on time arrival and departure onto the mainline from Margam’s Tata Steels large facility.
The key motive for this project stemmed from the lack of structured standardised ways of working being established in the outstation locations. This in turn was effecting the clients ability to service its customer base inline with its ambitions.
Our client engaged Project7 to lead this programme as they identified they did not possess the inhouse capability to achieve the desired scorecard and cultural improvements targeted, across their workforce.
Our client was trying to make a shift to a culture of Continuous Improvement across the business to enable a significant shift in performance. Due to being at the start of this journey the client did not possess the internal Continuous Improvement capability to Pilot and deploy improved ways of working across its locations.
Margam due to its size, location and the types of work it conducted had skilled engineering’s to work on the trains but no structure in terms of the planning, execution of the work meaning the overall Outstation capacity was far from optimised. The team at Margam possessed very little local improvement [Lean] capability and were nervous of what improvement meant and happy with their established ways of working not knowing.
Partner of choice:
- Project7’s demonstrable rail experience, success and trusted methodology for creating an internal capability coupled with our direct hands-on coaching approach were the main contributing factors for selection and being chosen as DB Schenker’s partner of choice for this programme of work.
In order to overcome the challenges within DB Schenker’s Margam Outstation and across its wider Network of locations, Project7 designed and supported the implemented a Continuous Improvement intervention Model. The model was designed to create the foundations in the identified Pilot locations, support the teams in deploying and demonstrating the benefits of the C.I. principles, systems and tools and coaching the team to continue the journey without the need for ongoing external support.
Project7’s coaching and implementation of the C.I. foundations in Margam covered the following elements:
- Designing, deploy and embed a Daily Performance Management System,
- Launch Workplace Organisation (5S) in a Pilot Area,
- Improve material management and control,
- Establishing of Project Management Techniques to enable effective management of improvement activities,
- Process Mapping of identified Train process, and creation of baseline standard ways of working,
- Problem Solving and,
- Knowledge Transfer to both the Outstation staff and Leadership supplemented by coaching of an identified champion to continue the improvement work.
- Open Defects reduced by over 45%
- On time departure improved by 37%
- CCM Assessment Completion improved by 80%
- Work completion to plan improved by 75%
- Hazard reporting and close out improved from zero to 5 per day
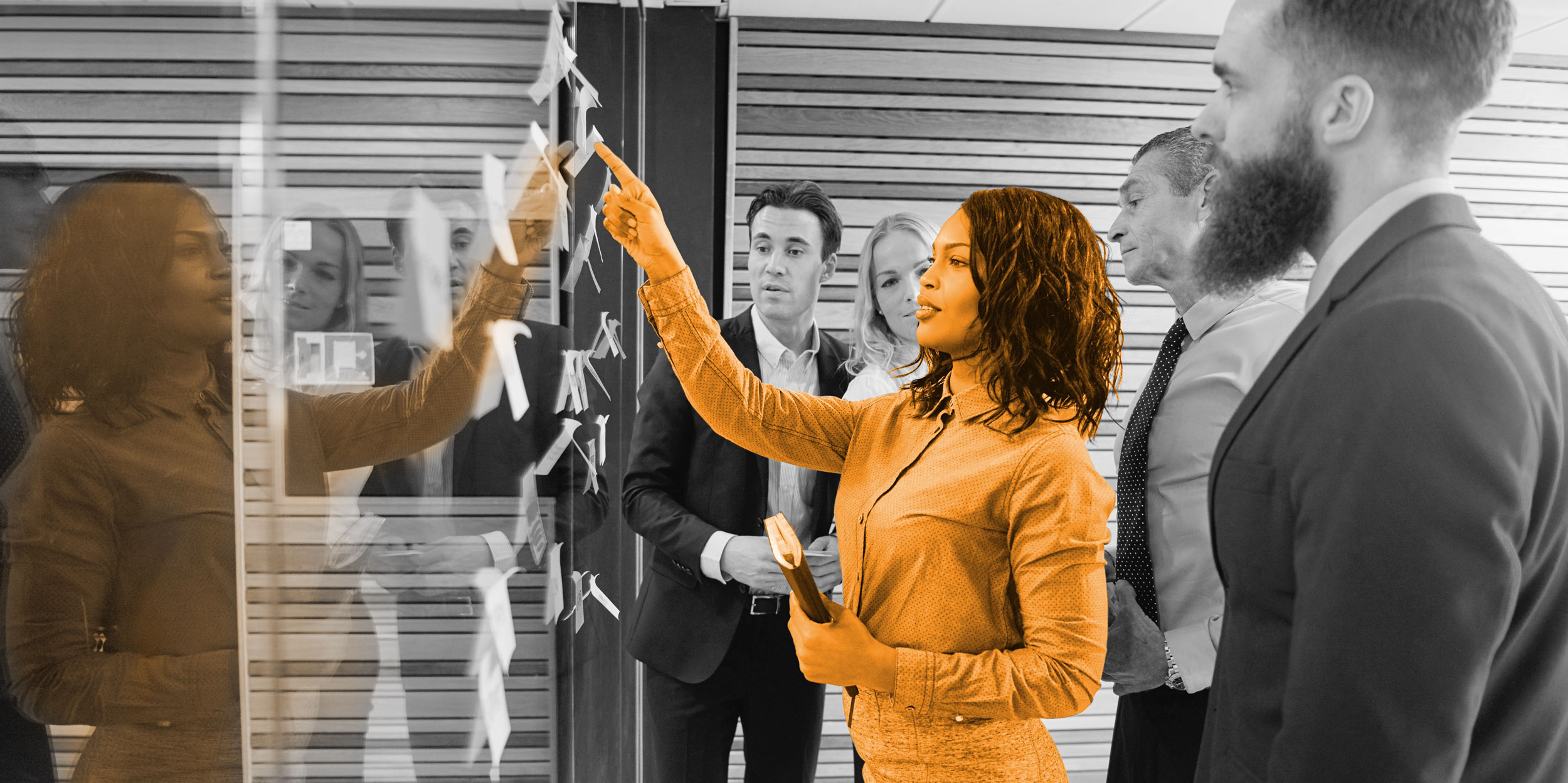
Lean Tools and Leadership Coaching
Grand Central (GC) are an open access rail operator in the UK, operating services on the East Coast mainline between Sunderland, Bradford and London Kings Cross. The GC fleet consists of ten five car Class 180 units which is maintained at Arriva Rail North’s (ARN) Heaton Train Maintenance Depot (TMD) in Newcastle since 2007.
Recent changes have seen the Light Maintenance of the GC fleet being transferred to Crofton TMD, which has enabled Heaton TMD to become the focal point for Heavy Maintenance.
GC’s strategic objectives for the Class 180 fleet is to ultimately increase engineering output and drive down cost, one of the tactical initiatives to generate revenue was to increase weekend train availability. The weekend train availability target was 6 units from 10, the target was to increase to 7 units from 10.
The immediate challenge for the maintenance team was to reduce the number of days it takes to complete a heavy maintenance exam from 5 or 6 days down to 4 days consistently so that the exam unit can be made available for weekend service.
Purpose: – to train and develop ARN Heaton TMD leadership team, Class 180 Production Manager and Class 180 heavy maintenance Team Leaders in leading a culture of daily CI. To help the leaders in establishing a leadership style that improves Class 180 heavy maintenance team performance, productivity and promotes daily CI through coaching,
Objectives: – to improve the quality, the output of the Class 180 16-man heavy maintenance team through the removal of waste from existing depot operations and maintenance processes using Lean principles and thinking whilst developing the team’s capability to ultimately achieve more with the same team.
Outcomes: – to have ARN leaders capable of leading performance improvement of Class 180 heavy maintenance through a structured Lean management system using daily Plan, Do, Check, Action [PDCA] and Lean problem solving through coaching, leading with questions and challenge.
The output of Project7 programme support delivered value for ARN Heaton TMD,
GC and the Class 180 heavy maintenance teams in the following areas:
- Developed ARN and Class 180 leaders who understand how to lead Lean and the daily leadership system in daily CI and effective Lean problem solving for Class 180 Heavy Maintenance.
- A Visual Performance Management Centre that provides improved, measurable performance in Class 180 Heavy Maintenance Safety, Quality, Delivery, Cost and People engagement in daily CI [SQDCP].
- A developed Class 180 heavy maintenance team who understand and can practically apply structured Pit-Stop Maintenance methodology to the heavy maintenance production line to identify and eliminate waste resulting in the reduction of time to complete maintenance tasks.
- Improved problem-solving capabilities and root cause learning for the Class 180 heavy maintenance team, resulting in increased process and operation awareness and effective problem corrective actions.
- Increased Lean thinking and technical capability of the Class 180 heavy maintenance leadership and maintenance team as Lean becomes habitual or ‘business as usual’.
- Creation of a ‘Centre of Excellence’ for the Class 180 heavy maintenance production line using Lean tools, techniques and associated behaviours.
- Class 180 Team Charter developed with GC & ARN & senior stakeholders to ensure clarity & alignment of objectives
- Class 180 KPI & metrics developed & deployed
- Class 180 Balanced Scorecard developed, KPI Tree & targets set based on SQCDP
- KPIs & metrics used to cascade objectives & performance reviewed daily
- Class 180 Visual Performance Management Centre
- 07:40 Structured Start of Shift briefings
- 11:30 Structured Daily Production Meeting
- Class 180 Pit Stop Maintenance carried out on A-Shafts & Air Dyers
- 37% improvement of time taken to complete on A-Shafts
- 59% improvement of time taken to complete on Air Dryers
- Full tooling & material lists created
- Class 180 Centre of Excellence
- Visual Performance Management & twice daily meetings
- Alignment & deployment of Class 180 SQDCP KPIs & performance metrics
- Process Confirmation developed and introduced
- Class 180 Lean Leadership Coaching
- 7 Habits of Lean Leadership Excellence profile
- TGROW Coaching methodology used for Rob Giblin
- Class 180 Material & Heavy Maintenance Planning
- Weekly Alstom HM material & planning meeting
- 7 / 14-day HM plan process developed
- 8 Week Look Ahead process developed
- HM Material delivery metrics developed
- Class 180 Open Defects reduced by 20%
- Class 180 Heavy Maintenance cost savings of £9k annually reoccurring
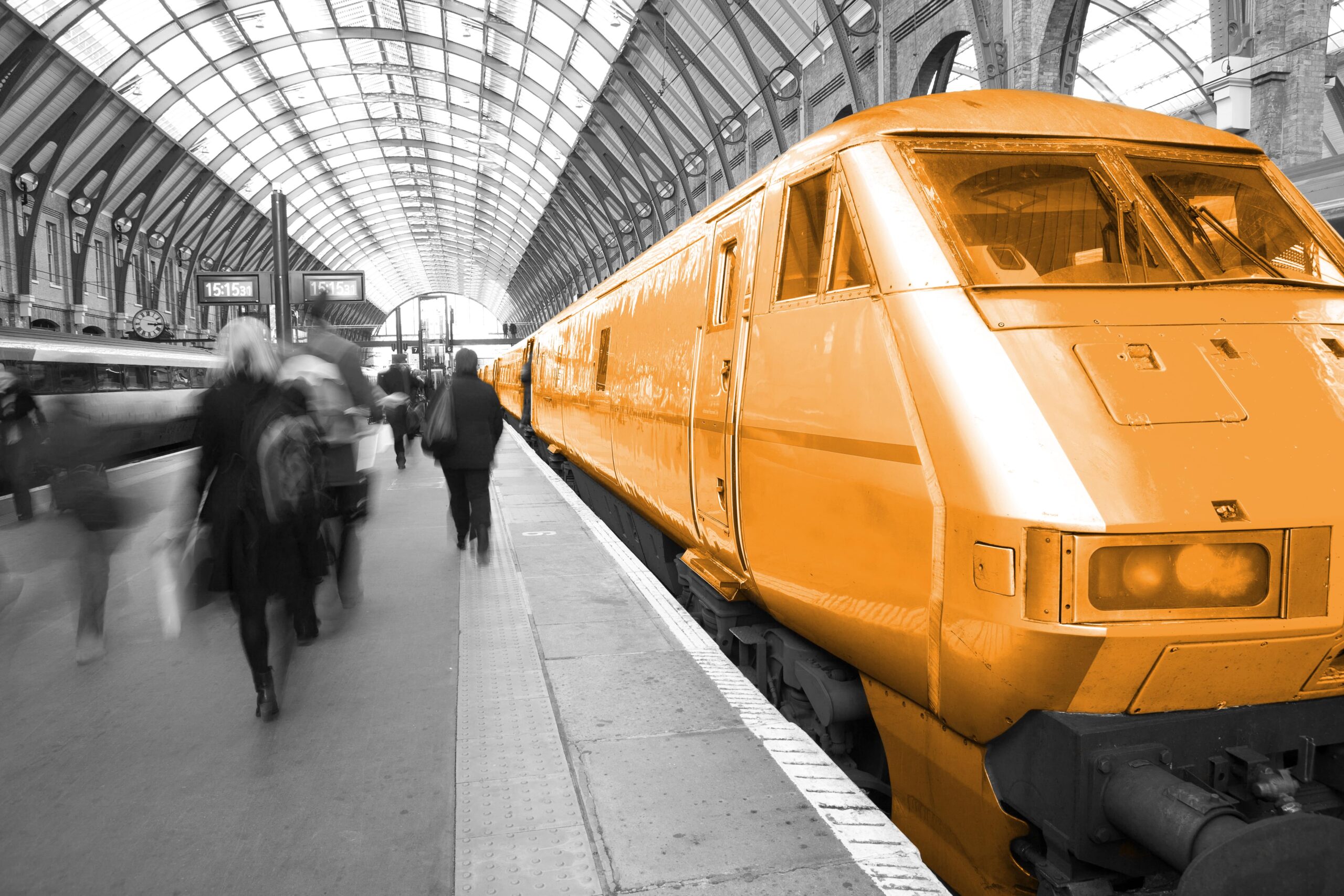
Transforming Scheduled Maintenance Performance
The client had a need to improve open fault performance. Open faults are defined as reported faults which after 7 days would accrue a pound (£) value every subsequent day until repaired.
The improvement project was split into two key areas;
- Performance Improvement
- Cost Reduction
LEAN Techniques below were used to track and improve performance and analysis of open faults to reduce reoccurrence.
- Visual Management of open fault tracking
- Process Changes to planning of maintenance tasks
- Practical Problem solving on repeat failures/concerns
- Regular governance of Key KPI’s
An initial analysis was undertaken to establish quantity and value of the current
situation across all areas of track and signals. Lines of communication
established between Maintenance, Engineering & Planning & Internal reporting of
open faults to establish ownership of failures.
Key elements of the project implementation process included:
Improved prioritisation of open fault by visualisation of top 5 concerns
• Weekly review with customer to demonstrate progress
• Development of improved and standardised working methods to enhance
performance levels
• Introduction of robust reporting and tracking
• Key engineering solutions to ongoing faults implemented
Over a period of 18 months open faults have reduced significantly in number giving the following results:
- Open fault values reduced by £11.6m to £296.00 (current)
- Currently 70% below the £1m KPI company target
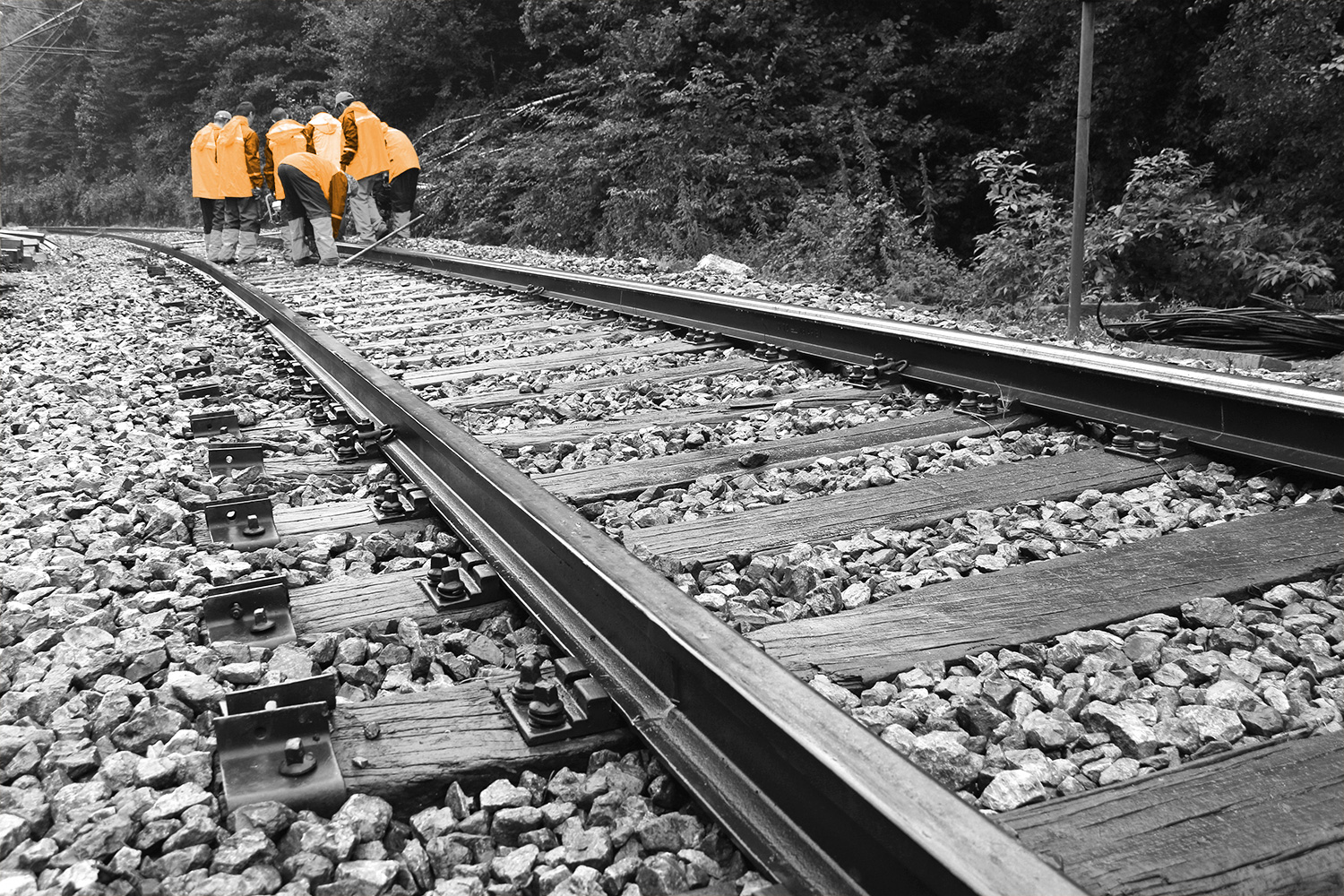
Stock Delivery Performance Improvement
The client is one of the leading train manufacturers, maintainers and train refurbishers in the world; employing 31,500 people worldwide with 23,800 in Europe.
The client was awarded the contract to refurbish the complete District Line 78 stock totalling 65 X 6 car units.
The client was encountering concerns delivering the required units on time to the customer, which was leading to high levels of liquated damages. On a required takt time of a 12 hour line move, the company was averaging a cycle time in excess of 28 hours to move the line.
Project 7 deployed a two phased approach to support the throughput. Firstly Project 7 trained leading methods engineers and production team leaders in 5 basic lean tools: 5s, Visualisation, 7 Wastes, Yamazumi and Kaizen. Following on from this class room training, Project 7 led the team through an on the job training program, which applied the classroom training in a real life situation.
- Line move time reduced from 28 hours to 11 hours. 61% reduction.
- Headcount reduction of 14 operators through waste elimination. 10% Reduction
- A total of £1,600,000 savings identified and implemented.
- ROI of 9 : 1 agreed
- Material cost reduction of £100,000 per unit set identified.
- 55% increase in lean manufacturing tools understanding.
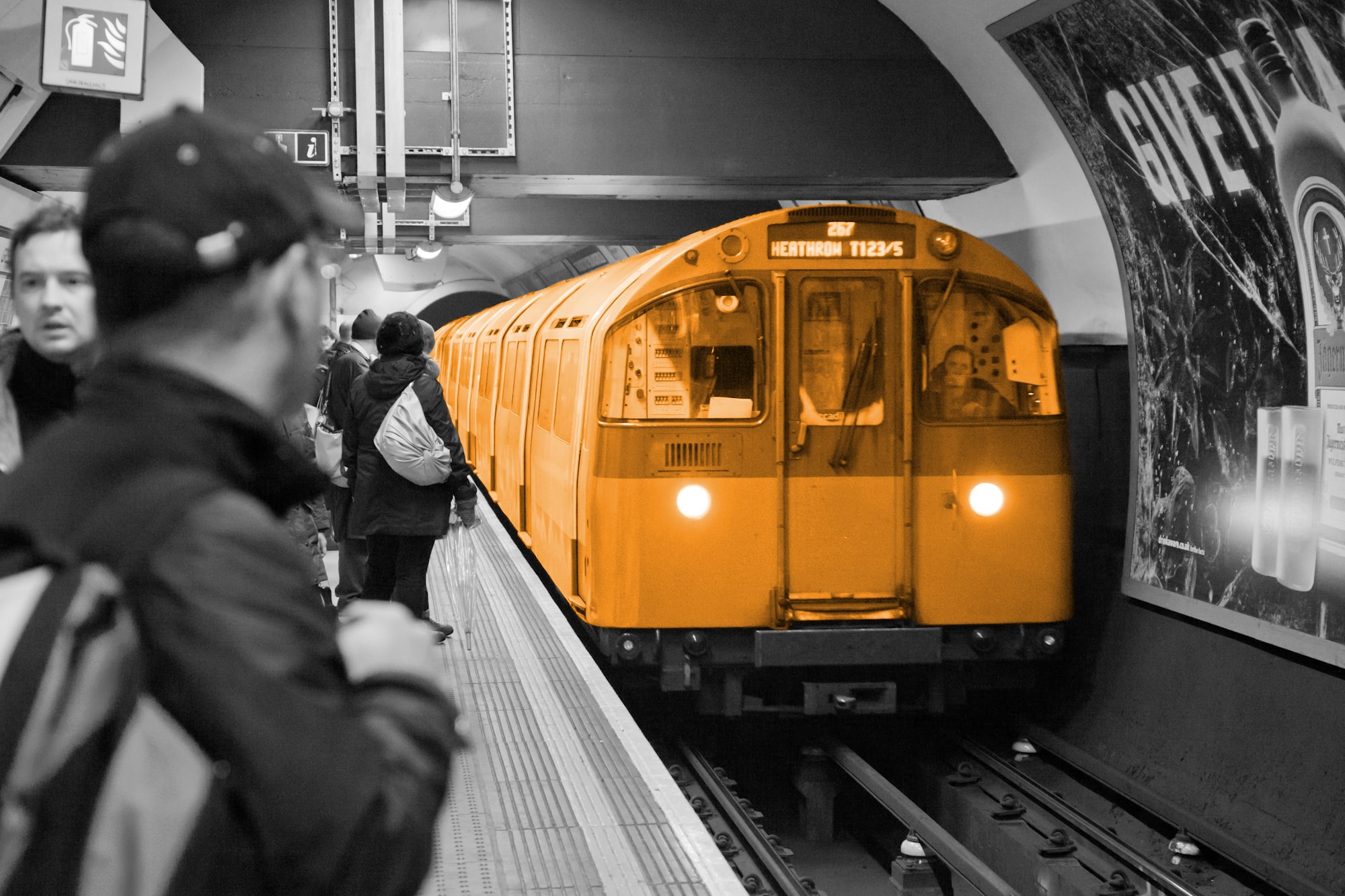
Fleet Management Transformation
The client has a presence in over 60 countries. It has an installed base of over 100,000 rail vehicles worldwide. The company offers the broadest product portfolio & is recognized as the leader in the global rail sector.
The fleet of modern 3 & 4 car EMU Electrostar* units running in the southeast of the England were underperforming through their daily unit availability.
The business was hemorrhaging an average of £124K per month to the Train Operating Company in Liquidated Damages through the Performance Regime contract for the year of 2005.
Working closely with the Fleet Management team to clearly structure the client needs, the performance improvements identified focused upon developing the organisation through the implementation of Lean techniques & operational best practice.
The performance improvement strategy centered on a Visual Management Operations Centre which focused on the Fleet Performance Regime Contract Key Performance Indicators.
Liquidated Damages reduced by > £100K per month.
Cost avoidance from Liquidated Damages for 2006 > £1M.
Visualisation aligned to the Performance Regime Contract.
Multi Functional Operations Centre created & sustained.
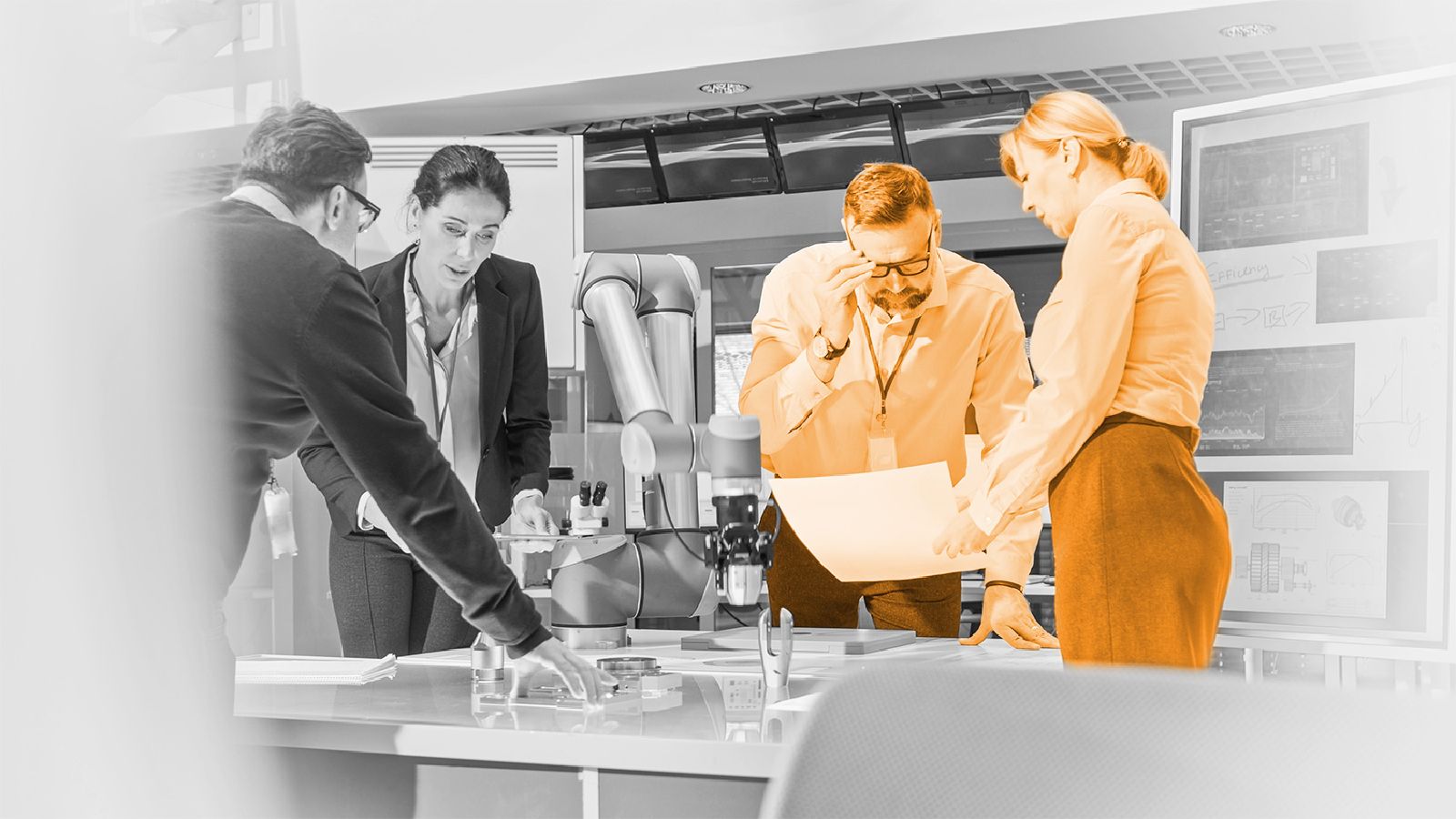
World Class Production Planning
Sydney Trains is the suburban passenger rail network for the city of Sydney, New South Wales [NSW]. In its capacity as operator and maintainer, under the Rail Services Contract with Transport for NSW [TfNSW], the railway covers over 815km of track, and 178 stations over 7 lines. In 2016- 17, 324.7million passenger journeys were made on the network.
The Sydney Trains Major Work’s division, part of the Maintenance Directorate, were undertaking a transformational reform project, working towards a target Operating Model to introduce new business units and facilities to their teams. The objective of reform was to create the catalyst required for a cultural and behavioural shift in mindset, to become a more commercially focused organisation, with an improved understanding of operational delivery and performance.
Project7 were engaged to assist the Major Works, Project Operations team to develop a Production Planning Process and coach the leaders to support the effective and efficient delivery of their annual works programme, across business units, through a defined standard that was transparent and would enable reporting of project planning status through Visual Performance Management.
Major Works division were impacting the operational performance of Sydney Trains significantly, through delays to the rail service caused by works delivery possession over-runs, which were predominantly due to poor planning.
Operating methods had evolved in line with growing demands on the rail network, and the business units had formed a silo working mentality. The impact of this, evidenced in planned works delivery, caused individual disciplines to have a distinct lack of coordination across teams. Project Operations, construction site management and engineering teams suffered programme and project losses, resulting in delays handing the track back to rail operations.
With the ongoing increase in service requirements on the rail network, the Project Operations team needed improvements across Safety, Quality, Delivery, Cost and People metric performance, in order to optimise delivery within shorter time windows, reducing possessions and their impact. In order to do this, a clear vision was needed, as well as a case for change, to ensure all employees were aligned to the business objectives, and fully engaged with and committed to delivering Continuous Improvement in their daily Production Planning process and job execution.
Key issues for Project Operations included:
- Increased cost due to repeat site work not being fully completed in the time available, missing materials and rework through poor quality workmanship
- Limited visibility of the work demand forecast from the annual works programme, leaving insufficient time to plan effectively
- Increase in Total Recordable Injury Frequency Rate [TFIFR] due to a lack of consistency across pre-work site inspection meetings and start of shift safety briefings
- An inconsistent and unstructured approach to planning, leading to under utilisation of resources
- Capability level of managers to produce the plan was not at the required level
- Communication within teams, across work groups and functions, was not at the required level
- No structured pre and post possession performance review process in place to understand actual versus the plan for possession work
From the diagnostic phase of delivery, Project7 developed a solution informed by understanding Project Operations ‘Current State’ processes and associated pain points. A ‘Future State’ mapping exercise was completed with delivery teams to identify the framework for the ‘Production Planning Process’ and meeting governance required.
Through Policy Deployment the Production Planning process became the criteria for determining how Project Operations translates and cascades corporate goals into actions, to where the work is performed. This ensures the operating strategy is consistently translated into more specific and actionable targets for staff at all levels. The Production Planning framework includes a set of process tools, documents, meetings, and associated behaviours; used to manage both people and process, in order to achieve results and drive continued improvement and learning. The system was built using the Plan, Do, Check, and Action improvement cycle as its backbone, gaining control and steadily raising the performance of the Project Operations team.
The approach allows set targets, goals, and objectives to be measured, across all elements of Safety, Quality, Delivery, Cost and People performance metrics. As an output of the process credible data can then be utilised within the Visual Performance Management cells at all levels within Project Operations.
The foundation of the Production Planning Process is based on standardised Visual Management planning boards across Track, Signals and Electrical disciplines of Project Operations, and is underpinned by weekly structured performance reviews led by asset discipline Team Managers. Team Leaders from each area are now responsible for providing and communicating a weekly status update on each of the projects they manage creating ownership and accountability for the process.
Project7’s coaches engaged with and helped guide Team Leaders in recognising clear actions against critical risks, across each of the defined ‘Gateways’ within the Production Planning Process. In turn, enabling Leadership to support and focus on key priorities.
Within Project Operations the Visual Performance Management cells were aligned with the Production Planning Process; outlining a series of lead and lag KPIs to monitor effectiveness and efficiency of the planned works delivery. On site, pre-works meetings and start of shift safety briefs were re-introduced. Field reports were also formed through a Short Interval Control system, capturing plan versus actual, against the key task for each of the construction projects.
As a result of the Production Planning Process implementation by Project7, Project Operations achieved:
- Reduced customer impact from asset-related delays to the rail service
- Improved track possession planning and decision-making, to minimising the impact of major periodic maintenance plans on customers
- Improved reliability and availability of assets
- On target and under budget delivery of the annual works programme across their asset base
- Reduction of maintenance costs
The 2016/17 Major Works Balance Scorecard results further demonstrate the impact of the Production Planning Process output, in support of the goals and objectives of Project Operations:
- Safety – Increase in on site safety briefings resulted in a 40% reduction in TFIFRs.
- Delivery – 1% increase in delivery of the Annual Works Programme.
- Quality – Reduced customer impact, with 10% improvement on post works asset related delays >5mins.
- Cost – Reduction in maintenance costs – net operating cost budget variance $13M under target for the year.
- Continuous Improvement initiatives identified $2.5M in opportunities for cost saving for the initial 12 months.
- The overall cost reduction equates to a 6:1 Return on Investment.
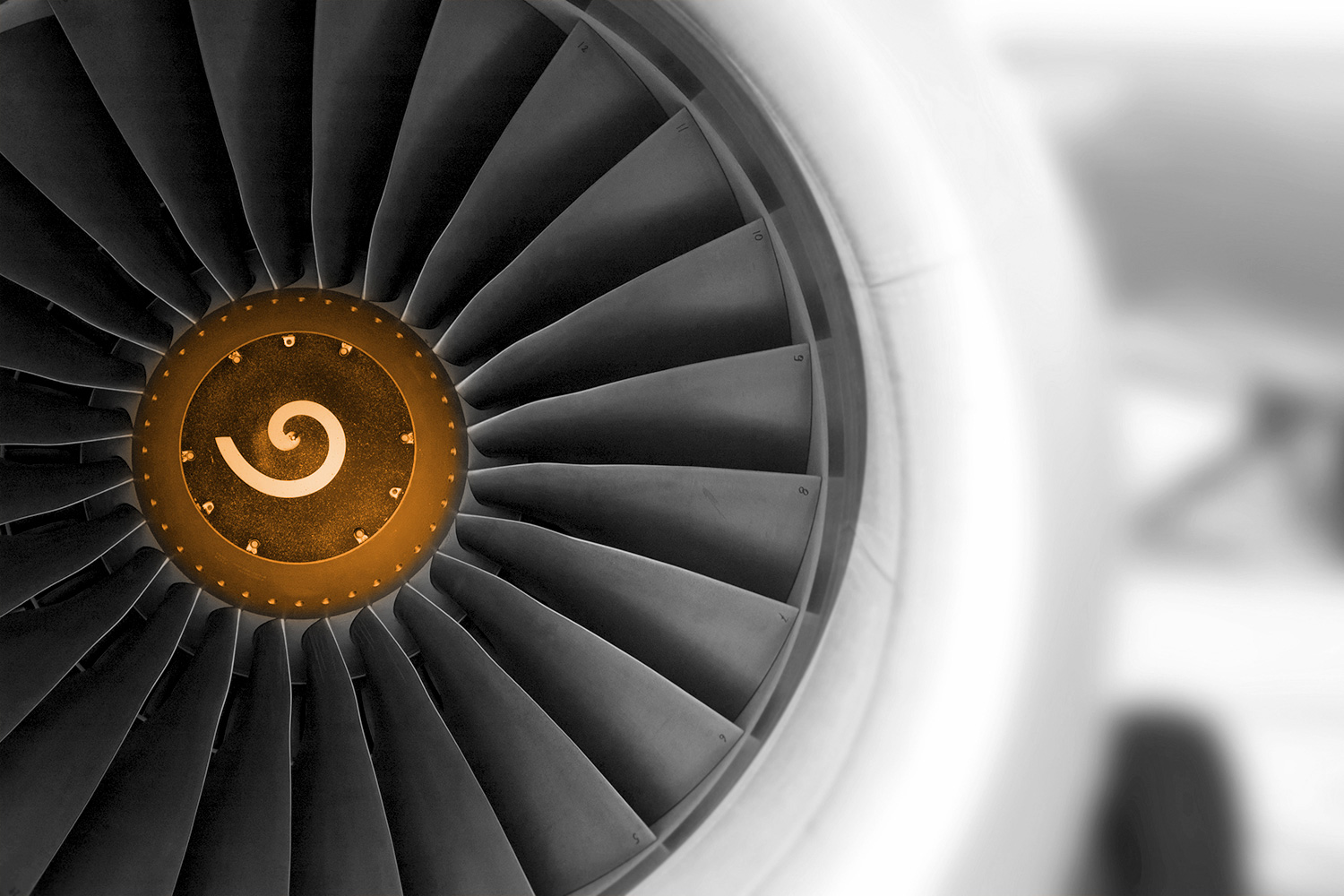
Enterprise Wide Operating Model Deployment
Lufthansa Technic is a leading independent manufacturer and provider of maintenance, repair, overhaul and modification services for civil aircraft with tailored maintenance programs and state of the art repair methods. They operate MRO Agencies with the capability to perform checks on customer aircraft at locations around the world.
Project7 was engaged in designing and implementing a Project and Performance Management Operating System to address underperforming Turn Around Times and poor schedule adherence and create the conditions for organisational sustainment by developing the Operating System guidance and benchmark standards to roll out across the Lufthansa European Agencies.
Lufthansa Technic had increased it’s European footprint through the purchase of additional strategic agencies. These agencies had differing levels of performance and challenges such as the cost per man hour. Lufthansa Technic wanted to drive improved, standardised way of working enable best practice to be replicated across the network quickly and tackle the performance gaps some agencies currently had. In addition to the above significant cost reduction targets had been cascaded to each Agency and our client wanted rigour and transparency of this to provide confidence and the ability to react quickly should any areas struggle to meet these challenges.
- Targets and performance was traditionally managed by the management levels of the business, without full accountability and any early warning system existing at an Technician level.
- Problem solving was adhoc with no systematic triggers to drive its structured application to business performance as well as technical issues.
- Although a mature internal improvement community existed, the level of capability and experience to design, deploy and coach in a full operating system did not exist.
Project Performance Management Operating System Rollout:
- Collaborative KPI and Target definition and cascaded from front line technicians to site Balanced Scorecard
- Visual Performance Management at every level, vertically and horizontally throughout the organisation
- Performance dialogues at every meeting based on the Visual Performance Management status and short interval control mechanisms
- Robust Process Confirmation by all leaders and managers to reduce variation and coach improvement
- Practical Problem Solving trained and delivered at all levels for repeat issues
- Leadership Development through Sensei Coaching practices [Kata TRGOW]
Creating the Conditions for Organisational Sustainment
Following the successful deployment of the Project and Performance Management Operating System, the challenge was to maintain performance standards following the direct Project 7 Consultancy support and create improvement benchmarks that encouraged continuous improvement in a standardised way across the entire Organisation.
We designed Lufthansa’s Organisational Maturity Assessment, improvement roadmap and Lufthansa concept documents for the Operating System. The assessment aimed to guide the same thinking way coached by Project 7 and addressed the physical deployment of the system, mindset, capability, and behaviours of the people. Project 7 successfully piloted the assessment and used the framework to coach the operating system with a Train the Trainer programme and our 4 Step Knowledge Transfer methodology. This systematic deployment ensured we built robust internal capability across the Process Specialist community and guaranteed long term sustainability.
The Organisational Maturity Assessment was defined and packaged to mitigate subjectivity when the teams deployed the assessment and establish an objective standard against which other Lufthansa’s Agencies could benchmark themselves. The increase of internal maturity and capability provided confidence to the Organisation that Project 7 could reduce its support and limit its involvement to conducting periodic evaluations and offer external calibration to the internal teams and Agency Network.
As a result of the deployment of Project and Performance Management and support from Project 7 the Pilot Agency which was once the lowest performing of the Lufthansa Technic Agencies became the best performing both in terms of quality, delivery and cost metrics.
- Throughput was reduced from an average of 46 days delay to an average of 5 days delay during a 17 day period with Project7 engagement.
- 89% improvement in Turn Around Time [TAT]
- Lead the European wide operating system deployment, with creation of a documented “How to” concept guide for use and further deployment.
- We directly trained 25 internal assessors to facilitate the assessment with 100’s of people coached in the Operating System through the execution of the Assessments by our teams.
- Baseline maturity increased from below Bronze standard to Silver in several areas, with firm plans established to achieve Gold standard.